Are LLMs our version of 3D printers?
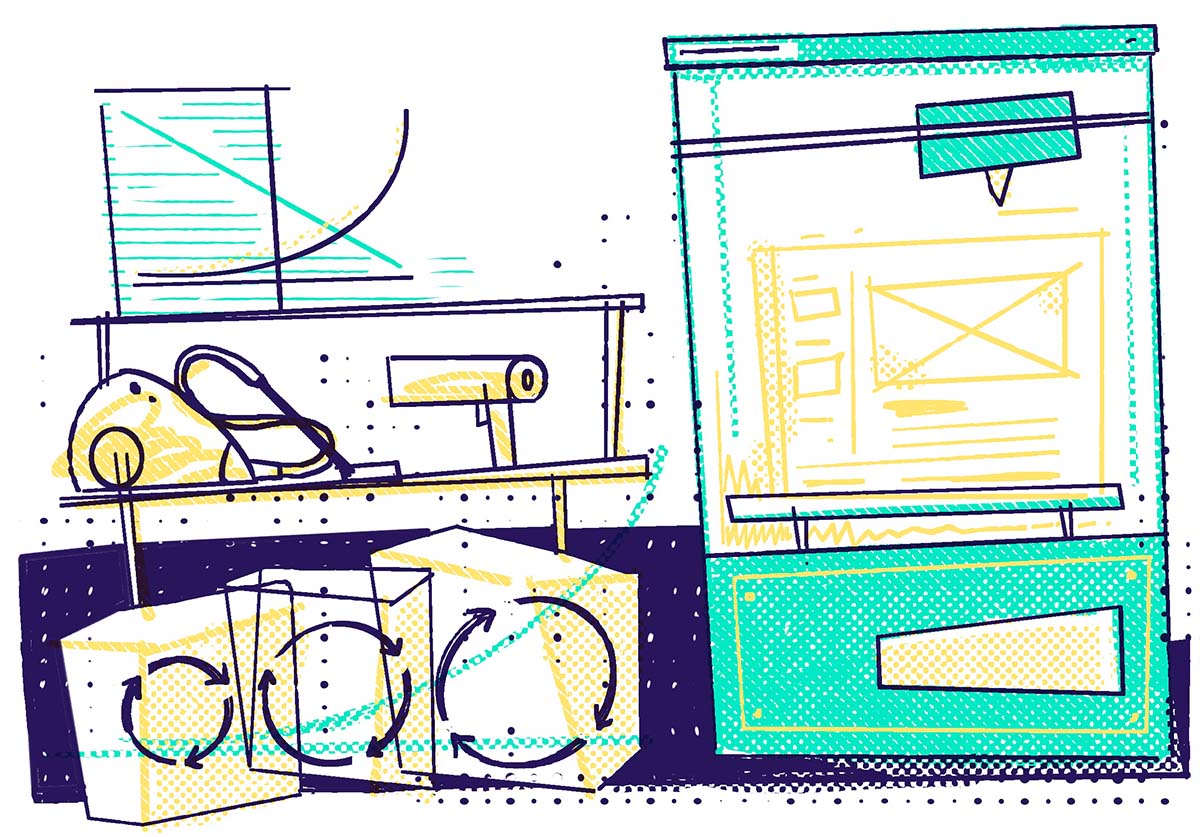
Director of Innovation
3D printers changed how physical products were designed and built. Engineers and designers could quickly iterate, test and validate ideas before handing over lots of money to manufacture the final product. Large language models (LLMs) are potentially the 3D printer moment for digital products.
In the past weeks an interesting conversation has been emerging about large language models being products that serve a niche purpose. Ken Mugrage, at ThoughtWorks, wrote a fascinating article on the topic. In brief:
- Generative AI’s future lies in niche applications since it offers new ways of interacting with large and complex data. We can see that with OpenAI’s move to plugins.
- Businesses should consider creating their own domain-specific models with self-hosting of LLMs starting to look viable. Those domains could range from customer support through to content creation.
- The success of LLMs will be by their seamless integration into our daily lives, providing context-specific assistance without being intrusive.
The final point is a perennial hope for any of us working with machines. That concept of seamless human-machine interaction is the heart of the ‘ambient’ computing model that Golden Krishna popularised in The Best Interface Is No Interface: The Simple Path to Brilliant Technology
In this article I wanted to build on Mugrage’s article by suggesting that early-phase prototyping of digital products is one of the niches to explore. We’re lucky here in the Innovation team to have backgrounds across both physical and digital innovation so we can see how LLMs might be a positive-disruption in the way that 3D printers were.
3D printers changed physical products
Before 3D printers physical models needed to be hand-fabricated or would be produced using CNCs, soft moulding, or (if you had big budgets) injection moulding. More often than not the earliest version of a product would just be a cardboard construction because it was the easiest way to bring an idea to life.
3D printing had been about since the 80s but they started to become popular in the 2010s when a bunch of patents lapsed. By 2015 it would have been surprising to find a product design or model making team who wasn’t widely using the technology.
The pace of technological change was nowhere near what we’re seeing with large language models, but for manufacturing - that normally has product lead times of years, rather than months - it had a similar disruption. And hype. Nesta, in their 2015 predictions, hailed that it would change all 21st crafts.
With that hype there was considerable fear. There was concern that it would destroy a craft. Engineers believed that designers would create 3D models that could never be manufactured. Designers worried that engineers would just use 3D models to do the design work.
Some of that happened. But mostly what happened was an explosion in creativity. As physical product teams it was suddenly possible to test models that felt - and looked - realistic years before they were manufactured. It was possible to change form factors, interactions and capabilities because experimenting was a factor-of-10 cheaper than it had previously been.
LLMs will change digital products
Agile was an organising response to the speed at which digital products could be produced. In 2001 - when the original agile manifesto was published - digital products had low levels of complexity and were substantially faster to create compared to physical products.
Even in 2001 the production of a digital product was still the largest task. When Marc Andreessen was talking about software eating the world in 2011 writing the code for a digital product was still the largest, most expensive, part of the process. Over the past decade the complexity of digital products has grown.
Like 3D printing we can produce low-complexity, incomplete, versions of the final digital product - or aspects of the final product - that feel, and look, real at an earlier stage. Done right, that should enable us to take a more user-centred approach. We can test more, experiment more freely and reduce risk. The way we’ve been approaching our weekly projects - this website, the art of the AI prompt, redact/reduce etc. - have all followed a similar pattern to my days at Dyson where we were quickly iterating and exploring ideas.
Yes, I’m nervous - just like I was with the explosion of 3D printing - that some people won’t use the technology in the most user-centred way but mostly I’m excited to see what new experiences can be created by making it easier and faster to prototype and experiment.